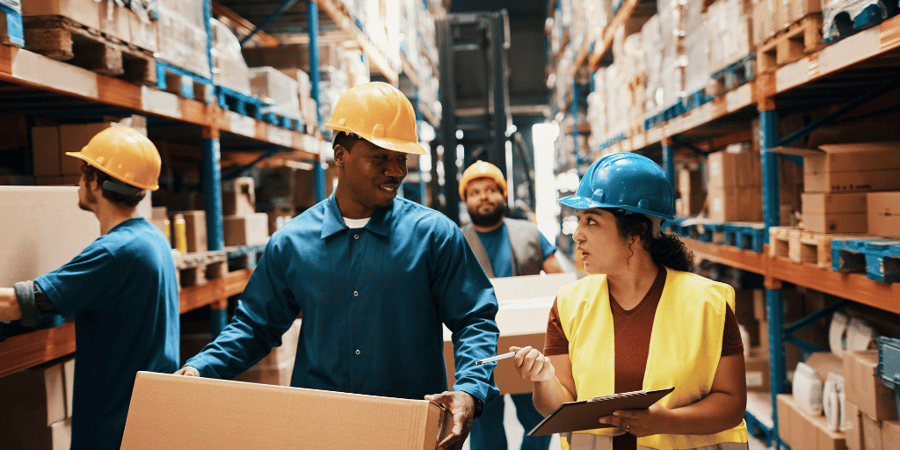
In a fast-paced business environment like the one we are in today, businesses must find ways to boost efficiency, minimize costs and maximize profits. The productivity pay model has gained immense popularity in the supply chain industry in recent years.
This strategy rewards employees based on performance and productivity levels and has succeeded particularly well in distribution centers.
The productivity pay model requires companies to incentivize their employees to work smarter. This, in turn, helps streamline operations, minimize waste, and improve overall productivity.
But what exactly is the productivity pay model, and why is it a big thing in the supply chain? Read on to find out more.
Supply chain planning and optimization
Supply chain planning refers to the process of strategically managing the flow of goods and services from the point of origin to the point of consumption.
It involves anticipating demand for products (and services) and planning their materials and components, production, marketing, distribution, and sale. Simply put, it's the process of planning a product or service, from raw material to final stages, including supply production, demand planning, and sales and operations planning.
Typical activities involved in supply chain planning include;
- Demand forecasting and management
- Planning production schedules
- Inventory planning and optimization
- Coordinating transportation logistics
- Collaborating with suppliers and distributors
On the other hand, supply chain optimization refers to maximizing efficiency and minimizing costs throughout the supply chain network. It involves analyzing and enhancing all aspects of the supply chain, including procurement, sourcing, transportation, production, and delivery, to achieve optimal performance.
Supply chain optimization balances the trade-offs between inventory levels, service levels, and costs. It also identifies opportunities for process improvements, production planning, inventory management, transportation routing, and network design.
Why is Supply Chain Planning Important in the Warehouse?
Supply chain planning, if done well, can help optimize product and food manufacturing and delivery. Since the supply chain is a crucial aspect of the operations of a warehouse, it must be well-designed.
The benefits of supply chain planning in a warehouse include;
- Better inventory management: Supply chain planning allows warehouse managers to forecast demand and ensure they have the right amount of inventory to meet customer needs. This also helps them avoid costs associated with stock outs or overstocking.
- Streamlined flow of goods: Warehouse supply chain planning involves optimizing warehouse layout, organizing inventory, and designing efficient picking, packing, and shipping processes. This lowers labor costs, reduces errors, and improves order fulfillment times.
- Reduced transportation costs: Supply chain planning allows warehouse managers to optimize the route of goods within the warehouse and coordinate transportation with other supply chain partners. This minimizes transportation costs and carbon footprint.
- Reduced operational delays: Supply chain planning in warehouses reduces operational delays across the supply chain processes. It fosters clear communication and collaboration among the warehouse staff.
What is a Vertically Integrated Supply Chain?
An integrated supply chain requires all aspects of the supply chain network to connect and work together seamlessly. It involves using technology and best practices to manage and optimize information, materials and financial flows.
With vertical integration, the business itself controls the supply chain and several stages of its production process. As a result, there are fewer (or no) dependencies on third-party vendors.
In a warehouse supply chain, vertical integration refers to the consolidation of different stages of the warehouse supply chain within a single company. For instance, it involves integration with;
- Material handling equipment providers
- Warehouse operators
- Transportation operators
- Staffing providers
There are two types of vertical integration: backward integration and forward integration.
Backward integration is when a company merges or acquires its supplier of warehouse-related goods and services like warehouse management software. This can help warehouse managers minimize supply chain disruptions and improve their control over the quality and reliability of warehouse-related inputs. It also ensures a steady supply of goods or services while improving coordination between different stages of the warehouse supply chain.
Forward integration involves a company acquiring or merging with its customers of warehouse-related goods and services like end-customers and transportation companies. This can help warehouse managers and companies improve their distribution and customer service capabilities. It also allows companies to better understand their customers and tailor their products accordingly.
However, vertical integration requires more significant investment and resources to manage the various stages of the warehouse supply chain.
Team-Based Productivity Pay Model
One of the best ways to maximize company productivity is by adequately compensating your employees. Employees who receive better compensation are motivated to perform and achieve organizational goals.
Companies have various ways of compensating their workers. Some pay employees based on hours worked; others pay them based on productivity.
The team-based productivity pay model has proven effective for many companies. It involves rewarding employees for their collective performance as a team. The company ties individual compensation to the team's overall success in meeting or exceeding productivity goals. With this compensation system, everyone gets paid equally.
The compensation is based on the employee's performance in completing productivity goals, like the number of trucks loaded.
The productivity pay model, also known as cost-per-unit (CPU) team-based pay, is among the most effective warehouse solutions for retaining workers.
CPU encourages cooperation and collaboration among team members—every worker's success depends on the whole team's success. Moreover, the approach fosters a sense of shared responsibility and accountability among team members. It also promotes a more positive and cooperative work environment.
However, warehouse managers should set clear communication and goals before implementing this payment model. Also, they should ensure a fair distribution of rewards. For instance, individual contributions to the team's success should be recognized and rewarded fairly.
Here are other benefits of productivity team pay;
- Increased performance
- Lower turnover rate
- Builds stronger leadership
- A healthier work culture
Productivity team-based pay has proven advantages for companies that want to control costs and increase throughput.
Want to Hear More About the Cost-Per-Unit Team-Based Pay Model?
Whether you're searching for a light industrial temporary staffing agency or a CPU-based pay model, we can help you recruit, hire and retain high-quality warehouse workers.
You don't have to go through the tedious and time-consuming process of finding and managing workers; we provide our extensive experience in general warehouse solutions to help you improve productivity and increase profitability. Contact us today to unlock the full benefits of using warehouse staffing agencies.