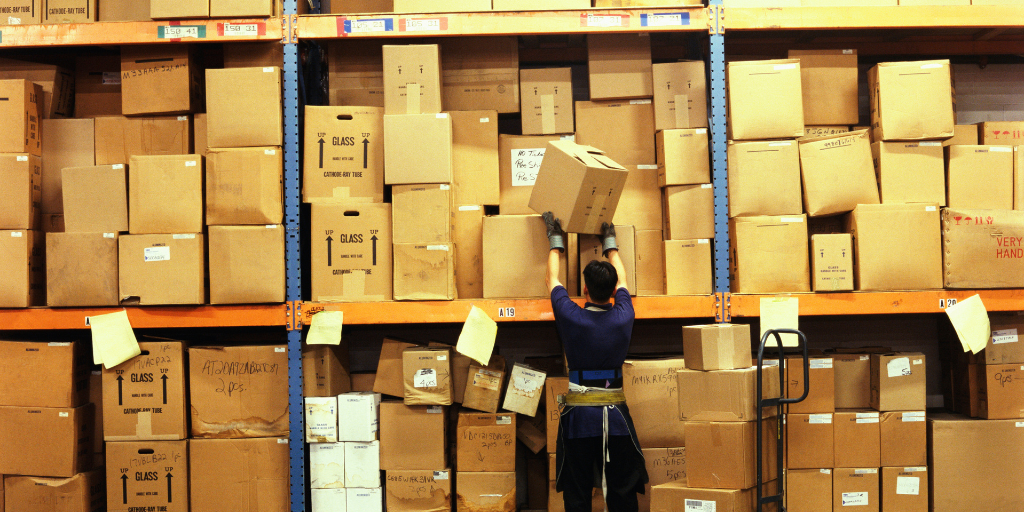
The global supply chain management market is projected to grow by 11.7% over the next six years, with many companies adding warehouses in the US to shorten supply chains and increase on time records when shipping to end users. If your warehouse operations are growing, you might be concerned about a number of factors including safety, productivity, sustainability, and efficiency. Rapid growth can lead to a larger number of inexperienced personnel who need training and are more likely to make mistakes. How do you scale up production without compromising safety and efficiency?
Some things to consider:
Assessing Current Warehouse Capabilities
You can't move forward without knowing where you are. Assessing and auditing your warehouse operations tells you what capabilities you have in your distribution center – and how well you are currently using them.
You may find that you have some opportunities for growth simply by identifying bottlenecks and inefficiencies in how you do things. Perhaps your staff could use a more effective system to determine routes through a warehouse when picking, or they might be slowed down by not having a sufficient number of vehicles. Removing these bottlenecks can give you the equivalent of growth cheaply. Make sure to include your senior employees in the audit as they are more likely to know where the real problems are than any inspector coming in from outside.
Leveraging Technology and Automation
Warehouse automation is a rapidly growing industry. It isn't limited to robots that pick, sort, and return goods, but also includes sensor and AI-based tools that help workers to perform their job faster. Automated storage and retrieval systems (AS/RS) reduce the number of workers needed and improve safety by keeping people out of tighter corners or by retrieving items from high shelves that workers might otherwise have to climb to reach.
Warehouse management systems (WMS) help manage the warehouse in a more effective way, including increasing picking efficiency, automatically tracking inventory and reordering supplies, and integrating with HR systems to better track worker hours.
Enhancing Workforce Efficiency
Safety and efficiency go hand in hand. Improving worker safety and developing a strong safety culture reduces downtime and improves morale, increasing productivity. If workers are not taking safety measures, it pays to look at why. Are they avoiding the use of fall protection because they are worried about it slowing them down? Are they taking unsafe routes to get to the break room faster? Overall efficiency is improved when workers don't take unsafe shortcuts.
Light industrial workers often need to upskill to work with technology and alongside robots. Making sure your employees get this training increases efficiency and attracts quality workers who are ready to adapt to new technology.
Efficiency also means improving scheduling to ensure coverage and giving employees adequate breaks so they don't become fatigued and make mistakes. Increasing the efficiency of existing, trained workers is safer than bringing in large numbers of new ones, and proper upskilling prepares them to train the next batch of new workers coming in. You also need to establish metrics to measure success and assess growth.
Optimizing Inventory Management
You don't want to have boxes and boxes of widgets, nor do you want to run out of supply. Inventory optimization is balancing these factors to make sure that your inventory is managed properly. This used to require a lot of guesswork. However, now, machine learning can be used to improve demand forecasting, rank inventory items, and ensure you have enough stock not to run out – and potentially lose customers. Modern technology solutions such as a proper inventory management system can help resolve these situations.
One thing the pandemic taught us is how vulnerable just-in-time inventory (JIT) is to disruptions. Fewer companies now use this tactic, but instead use a management system that involves careful choice of reorder points and similar techniques. Modern inventory management software is designed to help you optimize your inventory to save money, increase revenue, improve customer service, and reduce the need for more warehouse space.
Improving Warehouse Layout and Design
When was the last time you really looked at your warehouse layout? Too many companies fail to properly plan growth, but rather let it happen organically. This can result in a design that is inefficient and even unsafe. Improving the layout and design of your distribution center(s) is another great way to grow without a lot of capital investment in new buildings. You can effectively make your warehouse twice as big with proper layout planning, as well as making picking more efficient and integrating new technologies such as warehouse optimization software to improve picking routes and better manage inventory.
Ensuring Compliance and Safety Standards
Do regular safety audits and risk assessments. Include individuals who actually work on the warehouse floor in risk assessments, as they are likely to see things that managers may miss, and may have out of the box ideas. Audits should also ensure that you adhere to the regulations and standards for your industry, and to OSHA standards.
Invest in proper safety equipment, which includes proper footwear for all employees. Make sure that safety equipment fits and is comfortable. Historically, there have been issues with fit and comfort of safety equipment for female staff, which may be an area to improve in at your distribution center. Also, make sure that safety equipment is not just available for use, but is actually being used, and don't be afraid to make checks to ensure usage.
Safety training should be proactive and ongoing, rather than reactive or once in a while. When bringing in large numbers of new workers, you may find that classroom style training is the most effective, but also use on-the-job mentoring to ensure that they absorbed what they were taught.
Implementing Sustainable Practices
As you grow, so does your energy consumption, and with it your costs. Implementing sustainable practices reduces waste and helps your bottom line. More and more, people care about the sustainability practices of companies they work with and buy from.
If acquiring new sites, locations that are closer to retail customers and end users reduce fuel use and improve delivery times. New warehouses can be built to minimize the use of concrete and maximize natural light.
Not only can you make your new buildings more energy efficient, but you can make significant changes to your existing buildings. Replace incandescent and fluorescent lights with more effective LEDs, electrify onsite equipment such as forklifts, and add charging stations for your employees. Consider solar panels on the roof, which may be able to help with some of your energy needs and reduce your monthly energy bill.
Using a Flexible Workforce Solution
Sometimes, the solution to scaling up production in warehouses is an increase in temporary or permanent staff. Using an onsite flexible supply chain workforce solution allows you to increase your staffing levels quickly, decrease them during non-peak periods, and manage labor and scheduling better.
Eclipse IA's solution recruits light industrial workers who are familiar with unloading in warehouses. As more and more distribution centers start to use robots and smart devices, we can help you train your workforce to stay abreast of the latest developments as you grow, and we can help you do it in a way that allows us to customize those workflows specifically for you. We use a cost-per-unit team-based pay model that rewards productivity. We can slow turnover and handle it for you when it happens.
If you are trying to grow your business and need supply chain staff, Eclipse IA can help. We provide warehouse staffing solutions to help you recruit, hire, and retain high-quality warehouse workers now and into the future. Contact us to find out how we can help your business thrive.