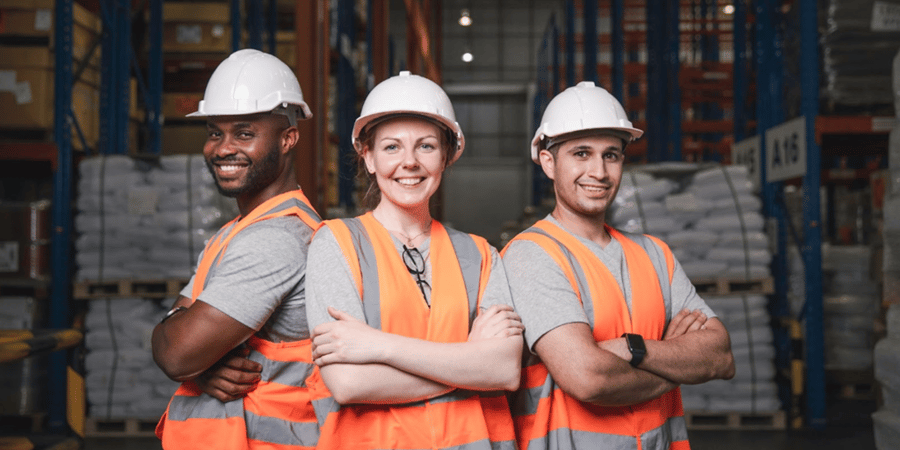
With the holiday season fast approaching and many suggesting that consumers will shop earlier than ever this year because of concerns over shortages, operations managers need to ramp up now to ensure they have enough staff to cover demand.
Often, warehouses staff temporary, seasonal labor during this time—but labor is in short supply right now. Also, temporary labor is hourly and unpredictable, with costs that can rise if overtime is needed. Typical expenses that may not be offset by revenue include:
- Staff on hand left killing time because they don’t have enough work to do, or…
- Not enough staff on hand to handle an influx of work, so overtime is required.
Why Are There Shortages of Warehouse Staff?
In very simple terms, it’s a matter of shrinking supply and increasing demand—an age-old problem. Baby boomers are leaving the workforce, and those entering now tend to pursue a college degree over trades.
At the same time, high growth in e-commerce, accelerated by the pandemic, raises the need for blue-collar workers, especially in transportation and warehouse settings.
According to Industry Week:
“The National Association of Manufacturers reports that a skills gap has caused about a half-million manufacturing jobs to remain open, and consulting company Deloitte predicts that by the end of this decade, as many as 2-4 million manufacturing jobs may go unfilled, putting $454 billion in production at risk.”
Turning to a Contingent Workforce
From the employer standpoint, a temp workforce represents an available pool of talent, already vetted by somebody else, that comes on board with no long-term commitment and limited employer liability because the agency serves in the traditional employer role.
Turning to a temp workforce can help companies manage the ebb and flow of demand, helping to ensure that investments in staffing do not go unutilized. And agencies typically bear the brunt of onboarding and training.
There are some drawbacks, however.
The biggest drawback—and greatest potential opportunity for you—is that temp workers are paid for their time, not their output. That means that no matter how productive (or not) they are, you’re paying for the hours they’re physically on your work site.
A better alternative: hiring on a Cost Per Unit basis.
What is Cost Per Unit Labor?
Cost Per Unit, a.k.a. productivity pay labor is a different way of thinking about paying staff. Instead of paying them by the hour for the time put in, they’re paid based on a cost per unit figure so their income is directly tied to their productivity.
In a warehouse environment, for instance, they might be paid a certain amount for every box unloaded from a truck. Which employee do you think would work harder for you:
- One making $14/hr. regardless of how much they get unloaded, or…
- One with the potential to make $18, $20, $22 or more an hour, based on how much work they’re able to get done.
Cost Per Unit labor is a win-win for all involved. Companies can not only cut their overall payroll expenses, but they can see an increase in productivity. Employees can see a pay increase and have the potential to work shorter work days in some cases.
At Eclipse, we take the Cost Per Unit concept one step further through a team-based structure with specific team values at its core. Our teams are highly incentivized to work collectively to meet a productivity goal. Each team member supports their coworkers to meet client requirements.
Below are typical results we see with our customers where a warehouse employee is on an hourly wage vs. working on a CPU basis with Eclipse AI.
Learn More
The Eclipse IA Managed Cost Per Unit (CPU) model uses a team pay structure. Using this method, we’ve seen client companies grow employee wages by up to 35% in hourly pay.
Don’t be caught off guard and short-staffed this holiday season! Use our guide, A Quick Guide to Productivity Pay, to learn how to improve efficiency and productivity while providing an environment where employees can earn more.